Use of the latest laser welding technology for cross members for the windshield
In a pioneering project, GEDIA used a laser welding process with the latest technology to manufacture cross members for the windshield for the first time. The cross member is assembled from hot-formed individual parts and must meet high load requirements in the vehicle while maintaining tight tolerances.
Together with the customer, our process development team focused on a joining process with low heat input. A low heat input has the decisive advantage that the component geometry suffers almost no welding distortion and thus ensures smooth installation in the body.
As part of the investigation, laser welding of the press-hardened joining partners was tested and it was quickly established that the required strength and weld gap bridging of conventional laser welding for this geometry reaches its limits. This led to further tests of a process variant with filler metal in order to improve the joint strength, gap bridging and seam tracking. As part of extensive parameter optimization, the process was refined to such an extent that the customer's technical and economic requirements were met.
The experience with this first assembly was so successful that GEDIA is now using this process to mass-produce three vehicle programs for a German premium OEM and has already been commissioned for two further vehicle programs.
This project impressively demonstrates how quality and customer satisfaction can be increased by integrating modern welding technologies into production.
- Johannes Arens, Group Director Manufacturing Engineering
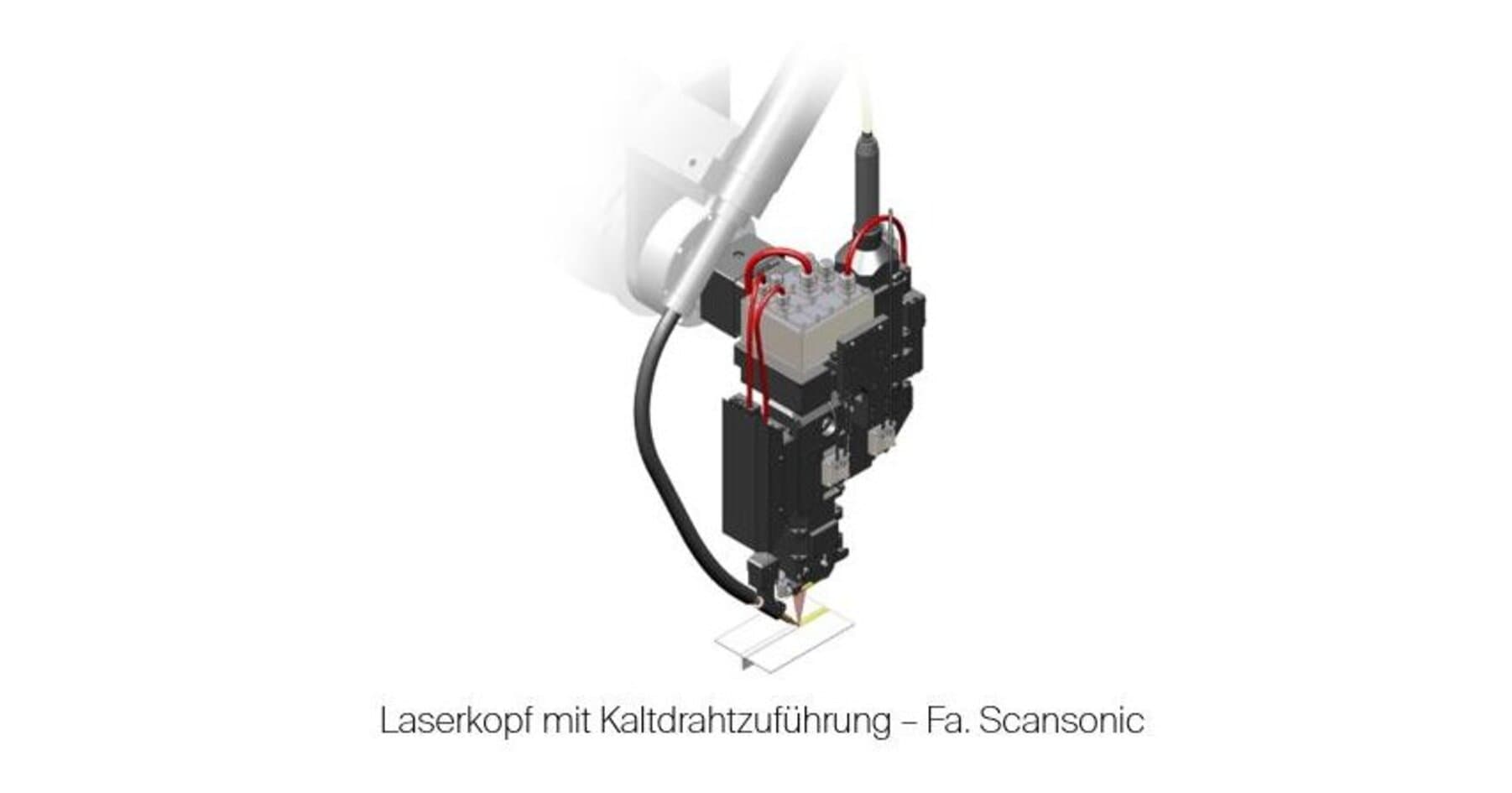