Use of CO2-reduced steels to reduce CO2 emissions in hot forming
The use of CO₂-reduced steels is an important step towards reducing CO₂ emissions in steel production. These steels are produced by using recycled scrap and lower-emission manufacturing processes such as direct reduction and electric arc furnaces powered by hydrogen and green electricity. Compared to conventional steels, CO₂-reduced steels have a higher proportion of by-elements, particularly copper and nickel, which enter the steel via the scrap and cannot be removed in the subsequent manufacturing process.
The investigations showed that the component properties of the CO₂-reduced steels are not significantly changed by the higher proportion of accompanying elements. However, the forming properties differ to a certain extent from those of conventional steels. Overall, however, the CO₂-reduced steels can be used in hot forming.
Another important point of the study was the analysis of the CO₂ reduction potential offered by switching to CO₂-reduced steels. It was found that savings of up to 80% of CO₂ emissions are possible, depending on the proportion of scrap in the manufacturing process. On this basis, a company like GEDIA could save up to 50% of its total CO₂ emissions by using CO₂-reduced steels.
These results show the great potential of CO₂-reduced steels from both an environmental and technical perspective. The use of these materials in hot forming offers a promising opportunity to significantly reduce CO₂ emissions without compromising quality and component property requirements.
- Sören Breuer, dual student in the field of mechanical engineering
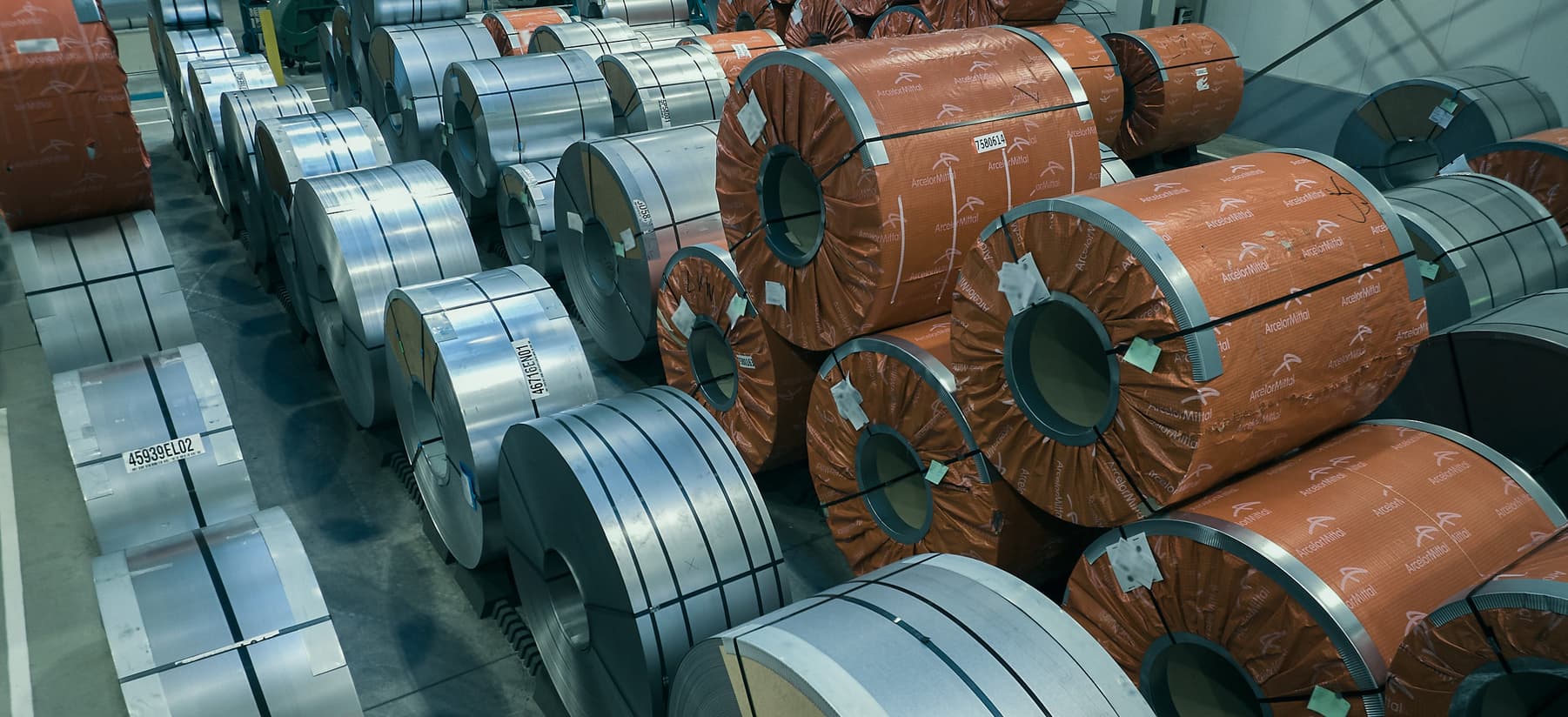